Crash, Electric Vehicle, Airbag, Tire, Engine, 4-post, Door slam, Thermal, Chassis, Suspension Testing
AUTOMOTIVE PRODUCT DEVELOPMENT AT ITS BEST.
Structural battery pack
The ability to easily determine the relationship between different components is one of the ARAMIS/ Pontos' easiest and best features.
Sled Test
During crash tests with dummies or airbags, non-contact measurements are needed to avoid distorted measuring results and measure data quickly. Thus, optical 3D metrology would be an ideal tool rather than conventional measuring systems like strain gauges. GOM outlines the benefits of point-based and full-field measuring 3D cameras that help improve displacement analysis and passive safety.
Side Impact
The optical sensors of the ARAMIS 3D Camera provide data of part and component geometries as well as of three-dimensional displacements and deformations. Static and dynamic deformations are determined based on individual points as well as on entire surfaces. With this measurement data, the safety and function of parts can be evaluated, and simulation and design processes can be optimized. The most interesting aspect for test engineers is how parts and components react during crash and impact tests – this is the only way to guarantee the safety of occupants and pedestrians. Therefore, a precise analysis of the dynamic behavior of individual parts and components is necessary. For this, point-based as well as full-field measurement techniques are provided. The camera is applied in crash and impact tests, wind tunnel tests, chassis and engine tests, vibration and oscillation analysis, and indoors, bonnet & closures testing.
Airbag testing
Strains in airbag housings and windshields full-field information relating to dynamic deformations is vital for components that are of relevance to safety. In consequence, full-field measuring systems are frequently used in crash and impact tests and component testing, for instance, on airbags and on tire test rigs. Airbag housing and airbag inflation characteristics are analyzed with high-speed cameras. The full-field measuring data is then used to calculate surface strain and planar displacements for all axes. Crash tests are another area in which full-field measuring systems are deployed, often for components such as windshields.
Engine Motion
The study focuses on understanding the displacements of the tube assembly throughout a specified load cycle. As specified by the customer, the locations of interest were quantified in X, Y, Z, and 6DoF (6 Degrees of Freedom) motion in 3D space.
The ability to easily determine the relationship between different components is one of ARAMIS/Pontos’ easiest and best features. ARAMIS/Pontos can easily reference any region on the part and measure any and all displacements relative to a specified body. Six degrees of freedom measurements work similarly where a component is isolated relative to another, while the directional displacement and angular change of the rigid body in 3D space are measured.
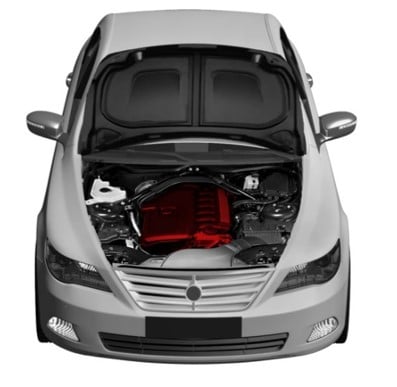
Windshield testing
Since the materials used for modern car windows consist of several material layers, numerical simulations are often inaccurate for determining their behavior under load. The full-field measuring data recorded by the ARAMIS 3D Camera can then be used to draw reliable conclusions on crack propagation in a windshield that otherwise stays invisible.
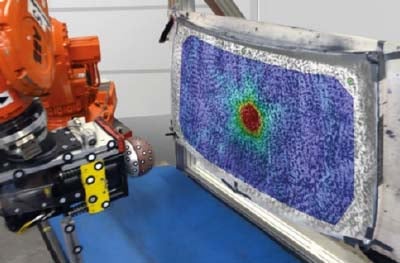
See the power of Optical Testing
Learn how our customers are benefiting
Wanna learn more?
Our team can discuss and demonstrate most of our products and applications virtually to you today!

Find out more about our latest automotive projects
1 min read
What is The International Digital Image Correlation Society?
Jan 23, 2025 by Ben Eisdorfer
1 min read
Unveiling the ZEISS T-SCAN Hawk 2's Revolution in Portable 3D Scanning
Jan 16, 2025 by Ben Eisdorfer
1 min read
Trilion Expands to a Larger Office in Novi, MI!
Dec 5, 2024 by Ben Eisdorfer