ARAMIS Optical Strain, Optical Motion, Adjustable, High-Speed, 3D, SRX
The Ultimate Digital Image Correlation Experience
3D Testing powered by ZEISS Industrial Quality Solutions
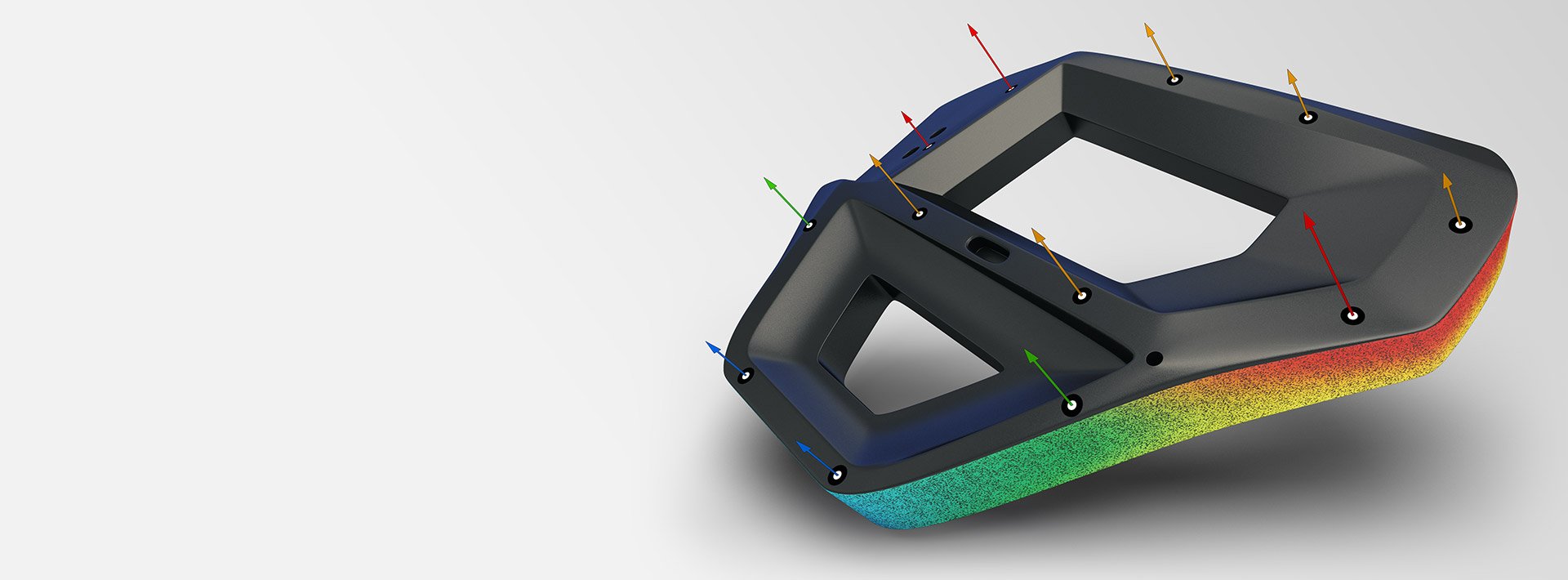
ARAMIS is a non-contact and material-independent measuring system based on Digital Image Correlation and Photogrammetry. It offers a stable solution for full-field and point-based analyses of test objects of just a few millimeters up to structural components of several meters in size. The system performs high-precision measurements with a 3D measurement resolution in the sub-micrometer range, regardless of the specimen’s geometry and temperature. There is no need for time-consuming and expensive preparation for statically or dynamically loaded specimens and components.
ARAMIS is a clear alternative for foil gauges and extensometers while being 10x cheaper than a traditional mechanical gauge, 50x less labor/time, and providing 100x more data. With countless applications from FEA validation, material/structural testing/SHM, and high-speed measurements, ARAMIS Optical Strain Gauge is being utilized for a wide range of industries from Automotive, Aerospace, Biomechanics, and much more, making it the first tool of choice when it comes to material and structural testing.
3D coordinates
3D displacements, velocities, accelerations
ARAMIS provides
Surface strain
Evaluations of 6 degrees of freedom (6DoF)
Adjustable
3D Fixed Base
High-Speed
Newest Member to the ARAMIS Family
ZEISS ARAMIS 1
Your Entry Point into 3D Optical Testing
ZEISS ARAMIS 1 is a powerful, entry-level 3D optical measurement system that brings you into the world of non-contact strain and deformation analysis. Ideal for users new to optical testing, ARAMIS 1 uses advanced stereoscopic camera technology to capture full-field strain, displacement, and deformation during quasi-static tests such as tensile, compact tension, and 3- or 4-point bending tests.
Discover more about the ARAMIS 1
ARAMIS Fixed Base
The latest camera technology with two 12-megapixel cameras provides a high spatial resolution. That way, not only small strain but also local strain effects in large measuring areas can be measured.
The robust housing design gives stability to the sensor and at the same time reduces the need for sensor calibration for applications in industrial environments.
The system can be used out of the box. The exchangeable camera frame and preset and certified measuring lenses allow for a fast adjustment of measuring areas.
Controlling the sensor using the ZEISS Testing Controller ensures stable communication between software and hardware. For high process reliability of the sensor, image acquisition can be monitored by the trigger assignment within the cameras.
ARAMIS 3D High-Speed
ARAMIS 3D High-Speed combines high-speed imaging with the power of the ARAMIS Optical Strain software to measure components at any speed, for high strain rate materials testing, vibration analysis, and impact testing, from thousands to millions of frames per second (fps).
Multisensor DIC Systems
Multisensor systems allow you to obtain synchronized measurements from various perspectives to then be analyzed in a common coordinate system. Through combinations of various sensor sizes and positioning, you can record global data for your strain and deformation analysis. ARAMIS is a full-field, non-contact measurement system based on digital image correlation that takes the guesswork out of traditional testing methods and allows you to test large areas of an object for evaluation. Multisensor DIC set-ups, like ARAMIS, can be used in various industries, including automotive, aerospace, and materials.
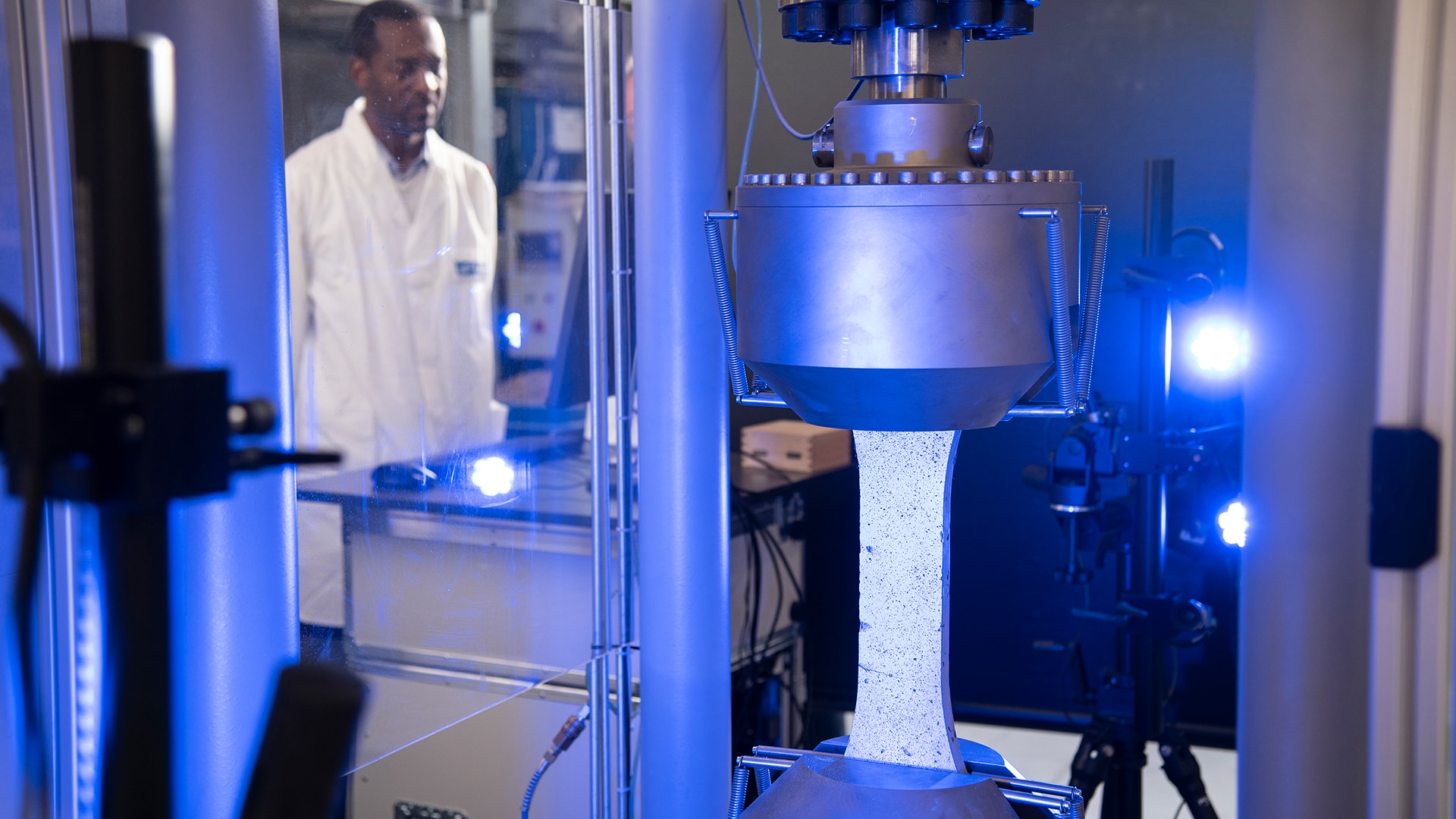
ARAMIS ACCEPTANCE TEST
ARAMIS optical systems measure strain with the ISO 9513's 0.5 class of accuracy, so it's approved for use in industries with higher accuracy demands. ARAMIS sensors' quality and performance capability are proven by the Acceptance Test (GAT), which is based on VDI standards 2634-1 and 2626. Customers receive a GAT certificate for the purchased sensor, a DAkkS certificate for the optical scale used, and a detailed process description.
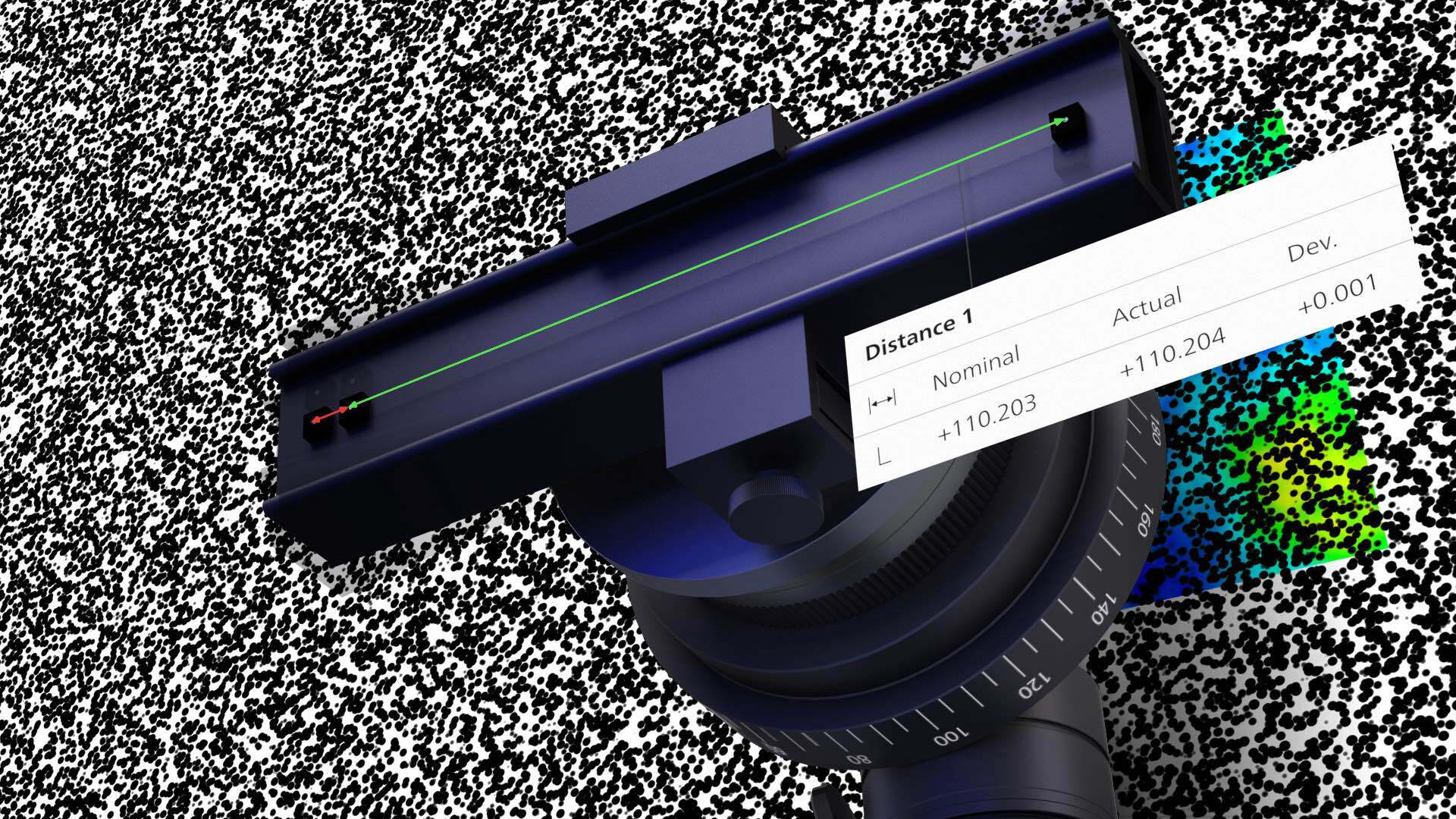
Upcoming Events
Recent posts
1 min read
ZEISS ARAMIS 1: The Standard in Entry-Level 3D Optical Testing
Ben Eisdorfer: Jun 13, 2025
1 min read
What is The International Digital Image Correlation Society?
Ben Eisdorfer: Jan 23, 2025
Want to learn more?
Our team can discuss and demonstrate most of our products and applications virtually to you today!