ARGUS Tool try-out, simulation validation, Material acceptance, Forming R&D
Optical Solution for Forming Analysis
RESULT BASED
Next-Generation Product Testing And Measurement
Trusted by Fortune 500 companies across a dozen industries.
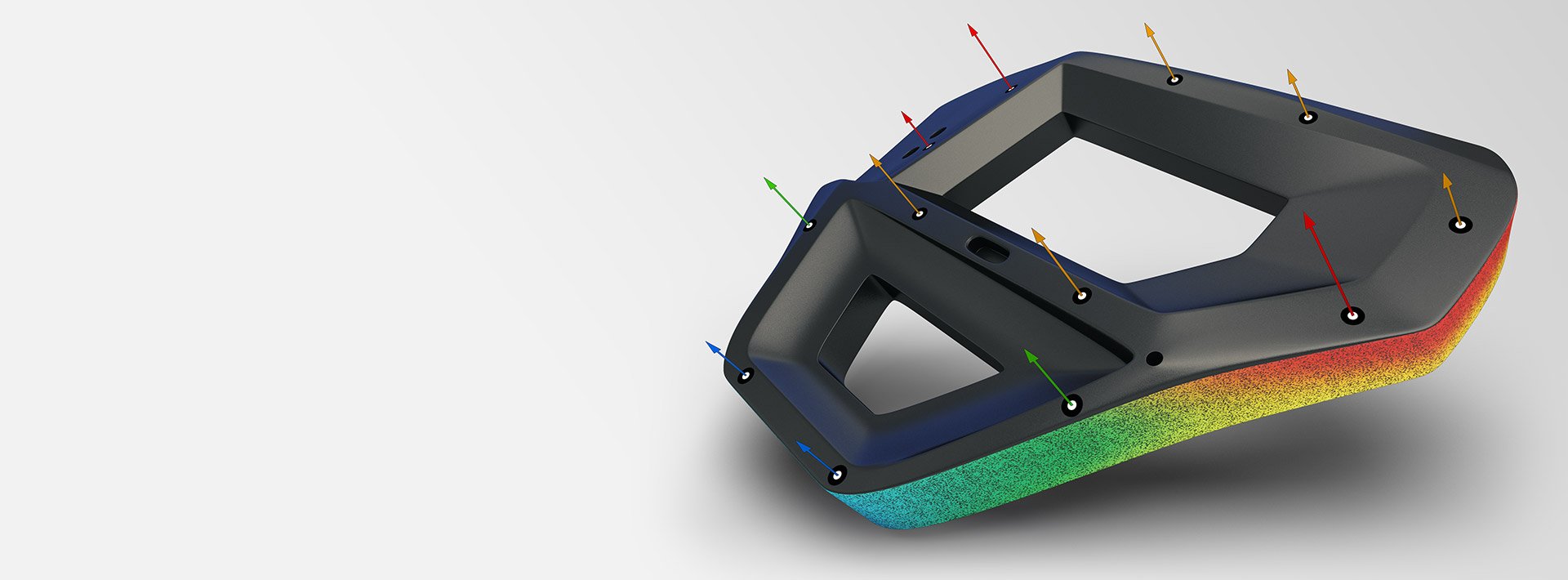
Highlights
Forming Analysis
Evaluate the forming states and surface strain levels of sheet metal parts after forming. GOM's ARGUS system clearly indicates whether the areas are over-deformed or still within a certain safety margin. This provides decisive information for optimizing forming processes, and validating simulations.
Easy and Fast
Unlike conventional methods for forming analysis, the ARGUS system provides an easy and fast measuring process and accurate forming results, even for complex and large parts.
Simple implementation
Plan
Before preparing the part, the measuring areas need to be defined depending on the evaluation purpose, which may be the complete part or specific critical areas known from the production process or numerical simulation.
Prepare
Before forming, raw sheet metal blanks are marked using electro-chemical etching or laser marking with a hexagonal dot pattern.
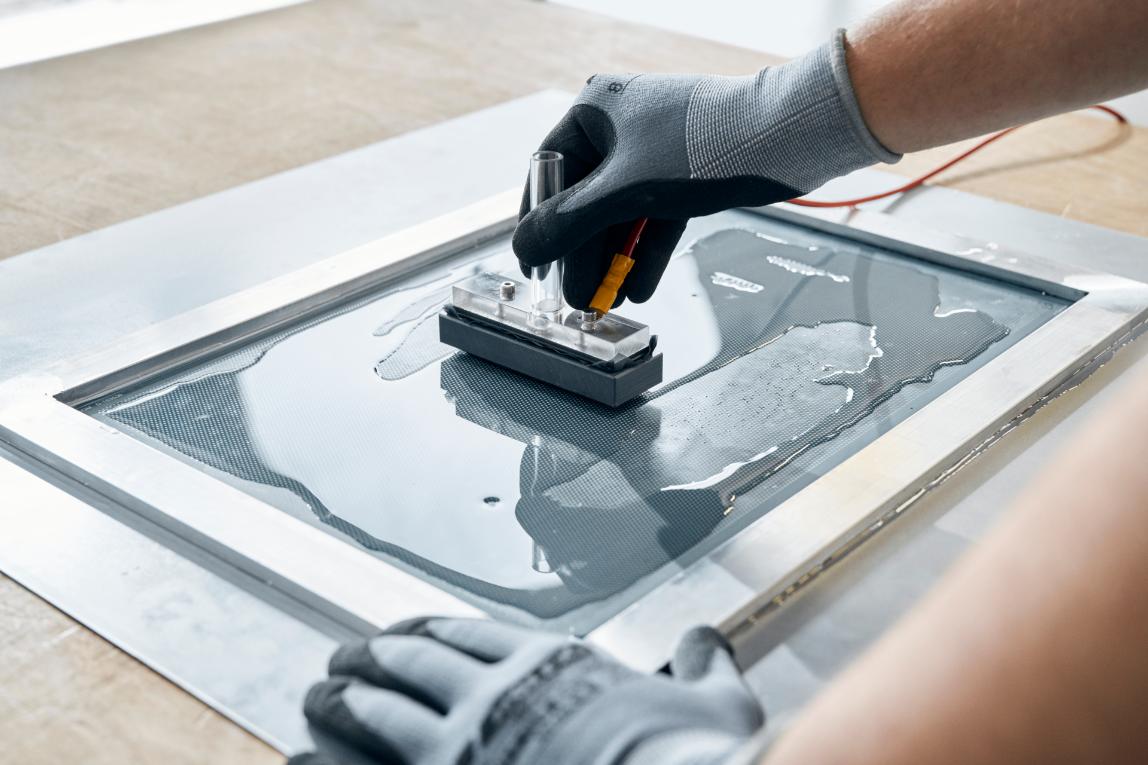
Measure
After forming, the sheet metal part is recorded from different viewing angles by using the handheld ARGUS system. Small and large parts can be measured very fast with the same hardware.
Evaluate
Measuring results provide full-field information of the forming distributions on the parts, like major and minor strain, thickness reduction, forming limits, formability, etc.
Evaluation of Forming Processes and Simulation Validation
The optimization of the sheet metal forming process, taking into account the correct material selection and tool optimization, is a decisive factor for competitiveness. This is particularly true in the automotive industry during the development process of sheet metal parts, for tool try-out, and in production troubleshooting. The forming analysis system ARGUS, supports such optimization processes, particularly by convincing and precise results of the surface strain on the components. The full-field results with high local image resolution provided by ARGUS enable the measurement of small and large components.
ARGUS Technology
The certified handheld ARGUS camera is used to record deformed sheet metal parts from different viewing angles. In all acquired high-resolution images, 2D coordinates of all dots are mathematically derived and recalculated to 3D coordinates using photogrammetry principles, taking into account ray intersections, camera positions, and lens distortion. The main result is a fine 3D point cloud, consisting of thousands of points, which represent the 3D surface of the sheet metal part. By evaluating the relative distance between the points in combination with a local plane strain tensor computation, the strains over the entire surface are holistically determined.
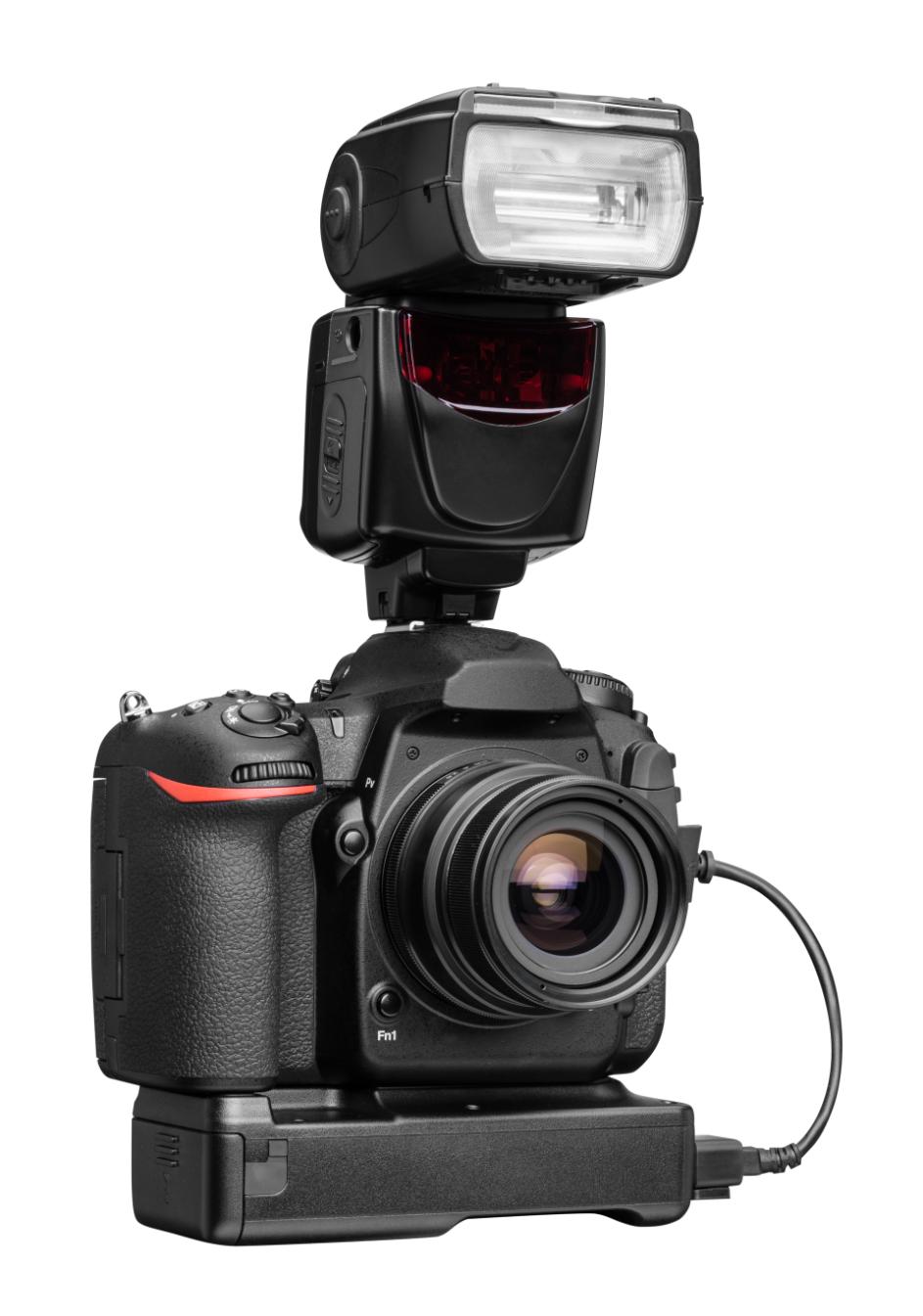
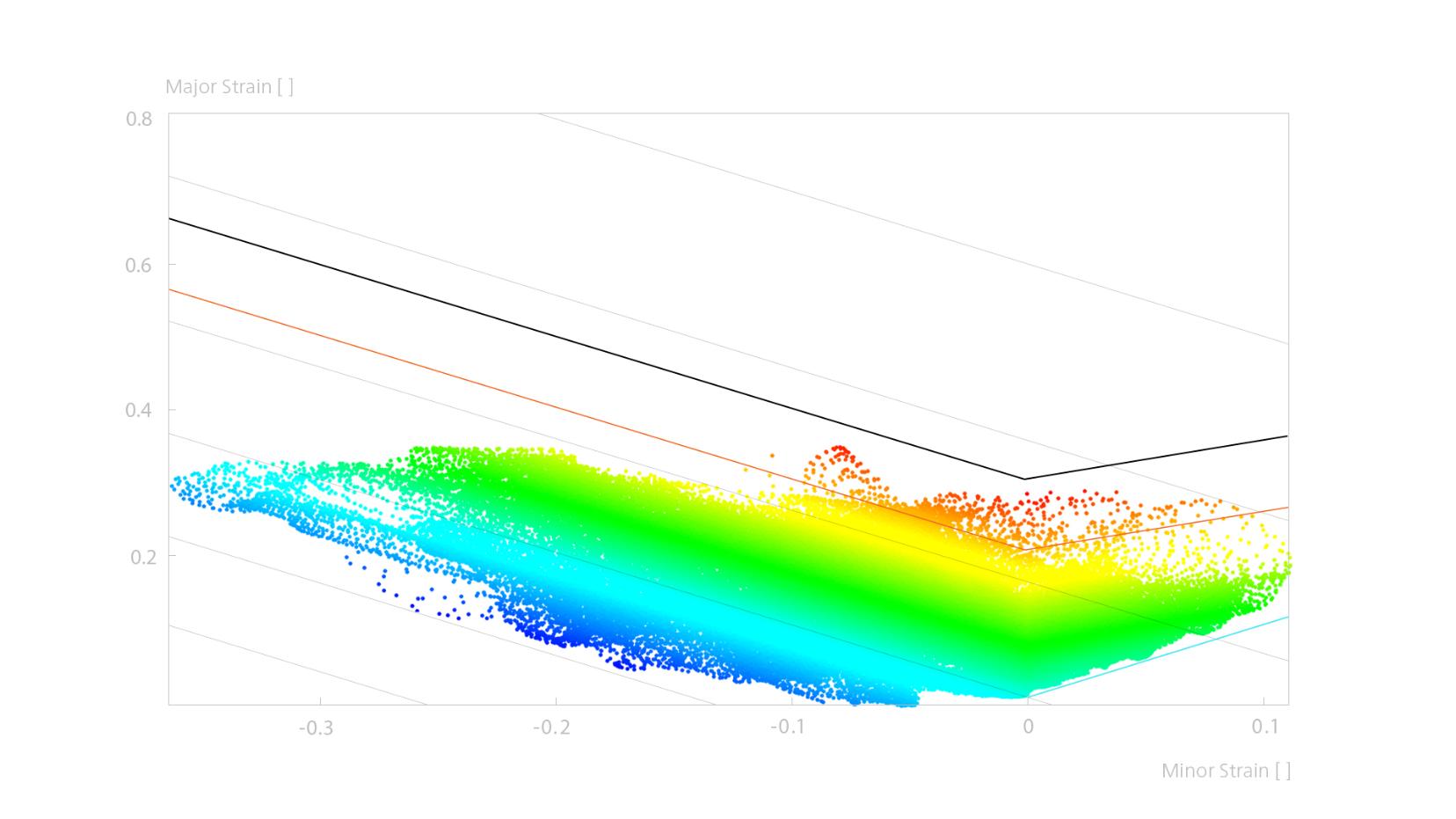
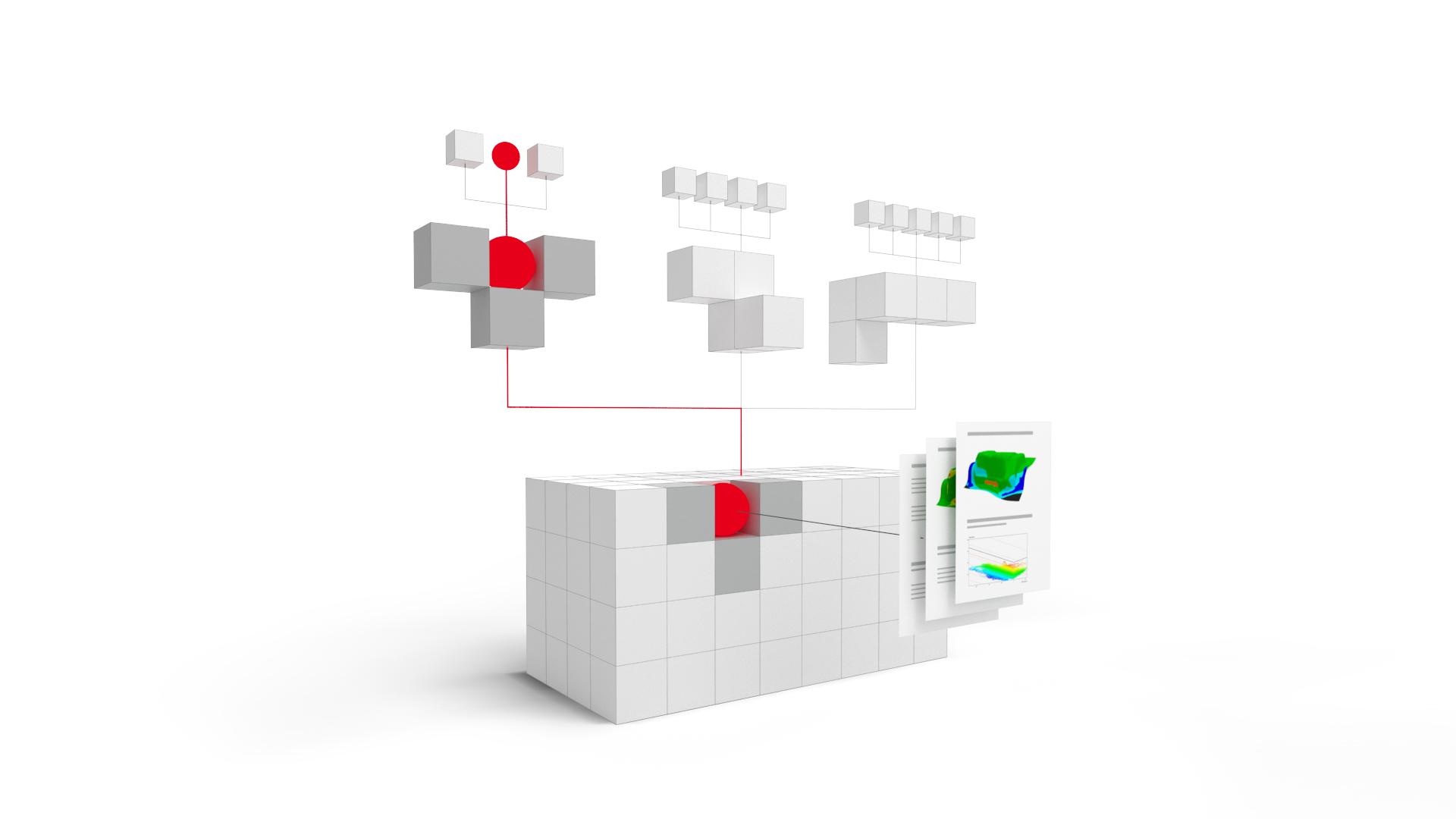
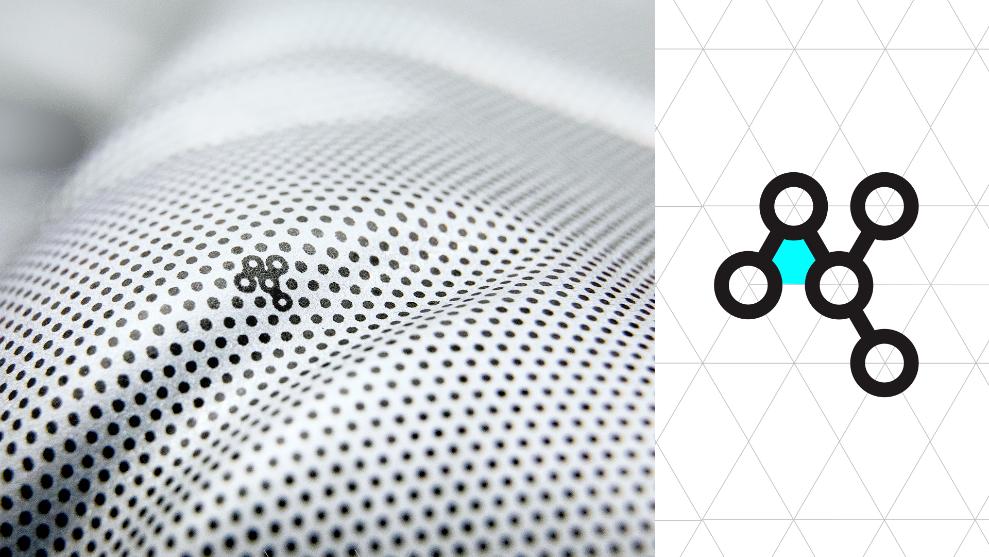
Forming analysis system
ARGUS supports the optimization of the sheet metal forming process taking into account the correct material selection and the optimization of tools. This a decisive factor for competitiveness, particularly in the automotive industry.
ARGUS provides full-field results with high local resolution for small as well as for large components. Therefore, it is ideal for numerous sheet metal forming tasks like: detection of critical deformation areas, solving complex forming problems, optimization of forming processes, verification of tools as well as verification and optimization of numerical simulations.
Furthermore the measurement system delivers full-field results for the verification of numerical forming simulations. The results from the ARGUS system provide full-field information about: 3D coordinates of the component‘s surface, Form change (major and minor strain, thickness reduction, Forming Limit Diagram (FLD), and sheet metal hardening.
ARGUS takes up conventional and proven methods of the forming analysis, which are based on the structuring of the blank. The measuring system operates independent of the material. It can be used to analyze components made from flat blanks, tubes or other components manufactured by an internal high pressure forming process (IHPF).
All results are presented in a fine resolution mesh created from the determination of the 3D coordinates and reflecting the surface of the measured object. In the Forming Limit Diagram the measured deformations are compared to the material characteristics of the blank (Forming Limit Curve).