Xi Analytics
A Manufacturing Revolution
RESULT BASED
Next-Generation Product Testing And Development
Trusted by Fortune 500 companies across a dozen industries.
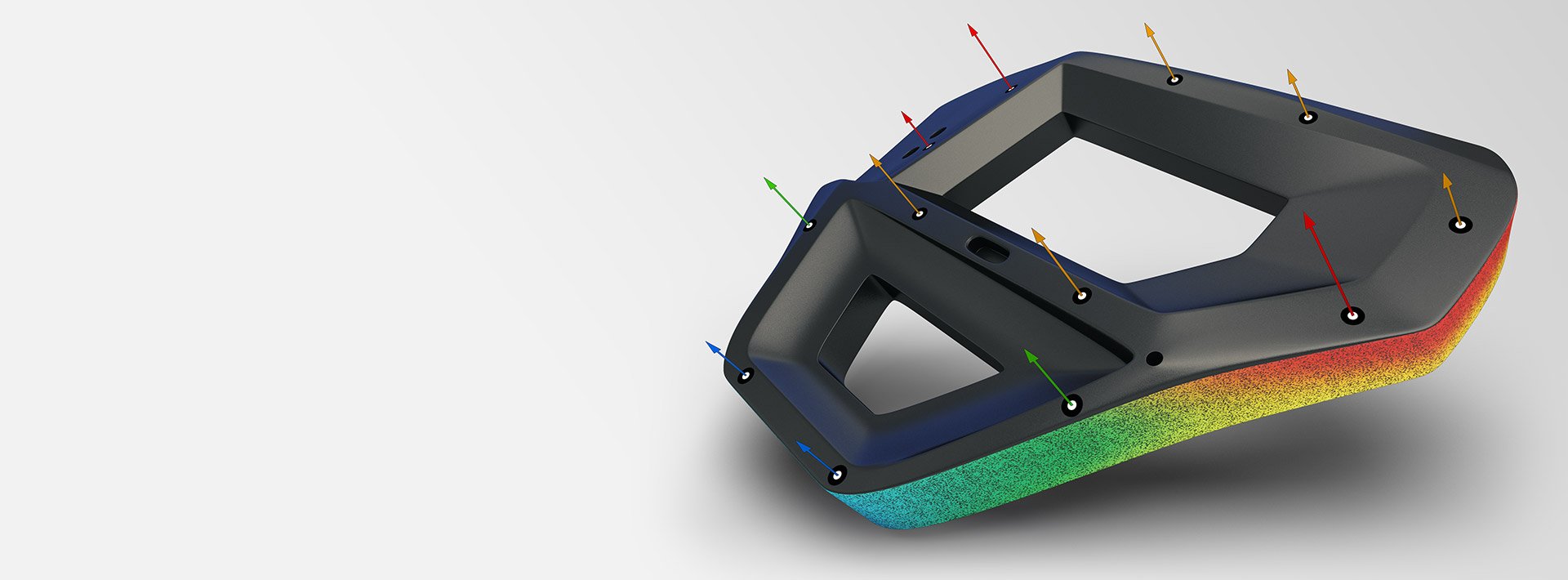
Tool-less assembly
No need to design, build and store physical tools
Digital Drilling
Each hole to be drilled is tracked to precise CAD dimensions, even on complex 3D parts, with Smart Tools. Blind holes can be drilled precisely, relative to reference structures, in true vehicle coordinates.
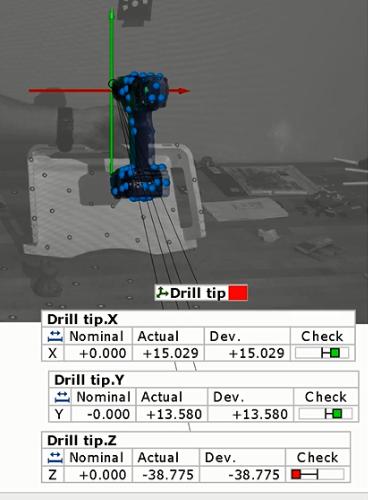
RVAT Kiosk for PONTOS Live
Build directly from CAD
60% faster than traditional hard tooling
QA (quality assurance) built-in
Precise positioning of components in 6-DoF (degrees of freedom)
Documenting as-built for your Digital-Twin
Xi Digital Twin
The Digital Thread records the As-Built details, QA, and testing to complete the Digital Twin and store it on the Xi Server for easy access and searchability.
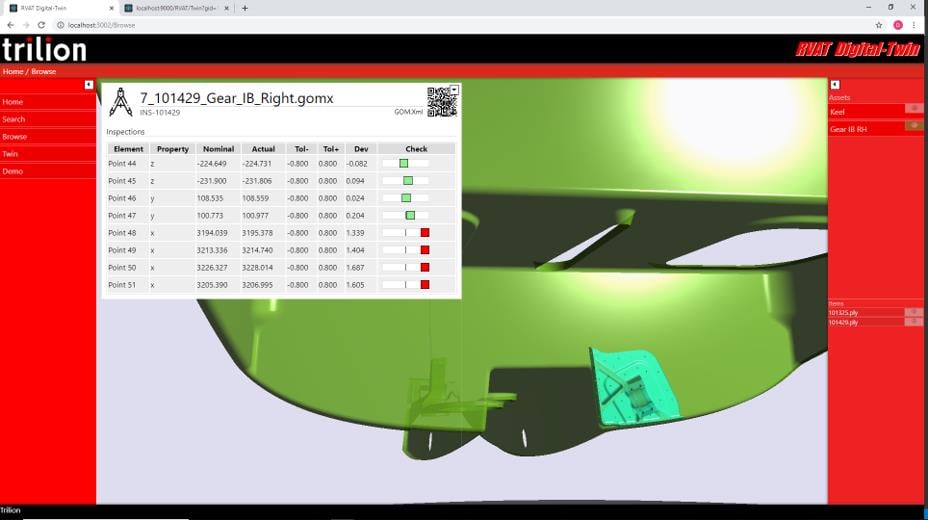
CoolScan Layup NDE
Voids, bridging and FOD can be detected before curing with our InSitu NDE during the layup to significantly improve product quality, ensuring high grade parts every time, and documenting these QA digital-threads for part validation.

InSitu AFP Layup NDE
Lap/gap, twist, porosity, voids and FOD can be detected in real-time with our InSitu NDE to detect problems during the AFP layup. There they can be immediately corrected to improve product quality and efficiency while reducing waste.
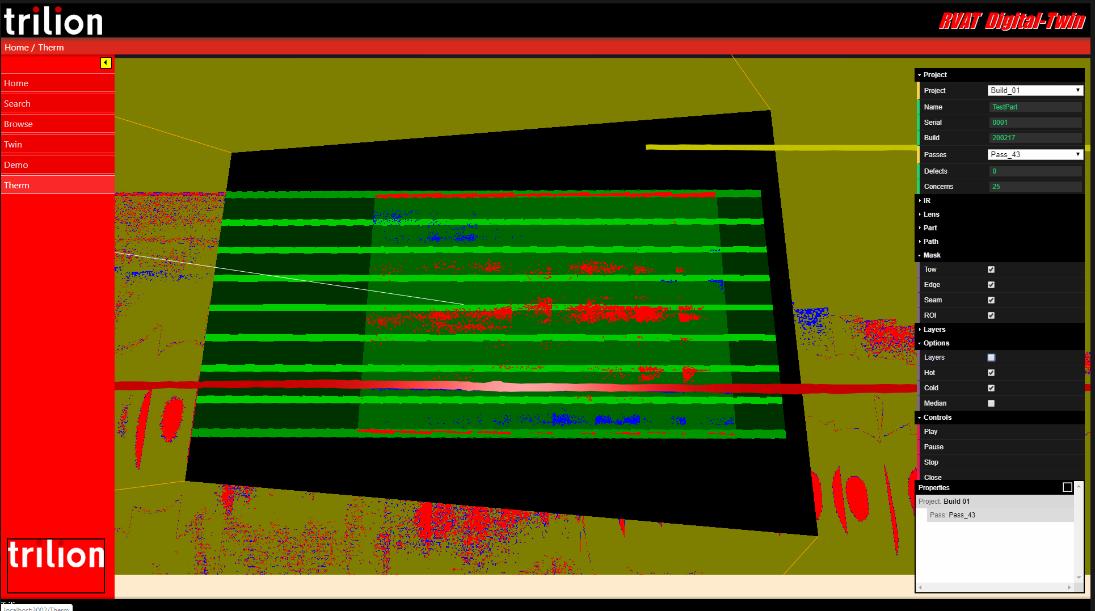
SmartTools
SmartTools allow the 3D optical tracking of standard or custom tools for precise positioning in true 3D CAD coordinates, in six degrees of freedom.

RoboTrack
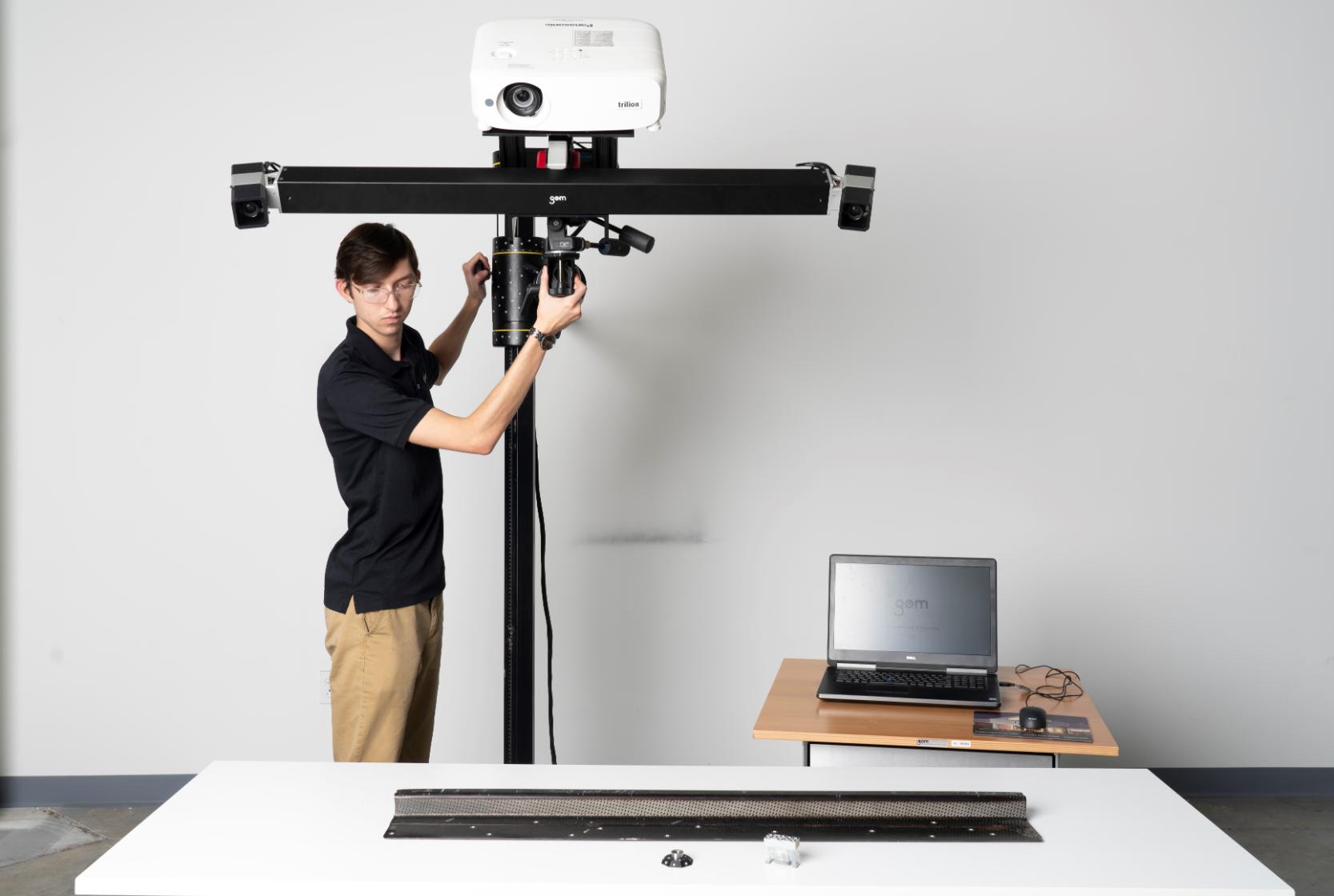